The Making of Carbon Monocoque
As you know,the process of building a carbon fibre monocoque is quite long and requires excellent preparation. It takes us probably around 3-4 months to complete the entire process with the techniques we use.Firstly, you will need to start with what is known as a plug. Basically, this is CNC machined from foam(sometimes another material) and is an exact representation of what the final chassis will look like. I have put a photo of the bottom half of our plug from last year below.
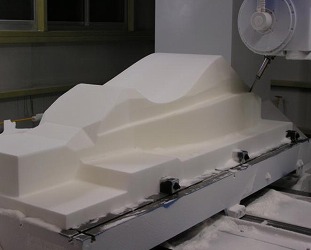
From this plug, a mould is then constructed. This is done using a high temperature fibreglass and resin, which produces an exact replica of the plug above. It is very important that the surface is perfect and no fibreglass is exposed, otherwise the carbon fibre will stick to the surface when you complete the final carbon fibre chassis.
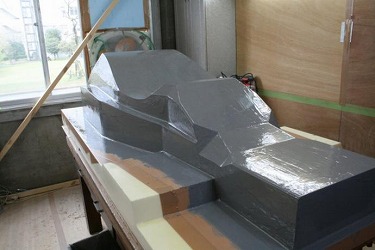
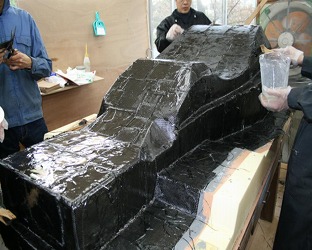
The surface then needs to be treated with either a wax or frekote so that the carbon fibre won't stick when the chassis needs to be removed from the mould above.
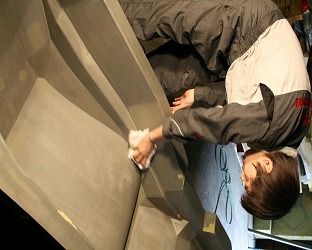
You are now ready to lay-up the carbon fibre. You start by laying an outer skin of carbon fibre into the moulds above. This basically forms the outside surface of the chassis once it is completed. Most teams runs between 2 and 5 layers of carbon fibre in the outer skin.
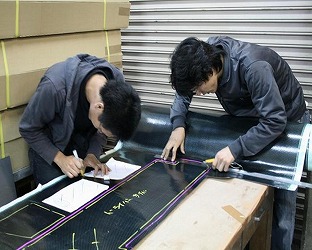
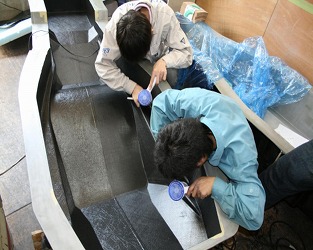
Honeycomb is then placed over the top of the outer skin. This is normally 15mm or 18mm depending on individual teams.Holes must be cut into this for the hardpoints such as suspension, engine mounts (basically anything that needs to bolt into the chassis). Some teams use Bakelite inserts, and some a 6000 or 7000 series aluminium depending on where the insert is positioned, and whether it needs a thread to be cut into it (such as for engine mounts).
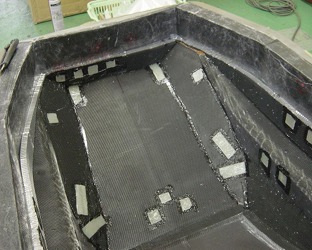
An inner skin is now placed on top of the honeycomb to form the inside of the chassis. This is again typically 2-5 layers of carbon fibre. Once this has been completed, the chassis needs to be vacuum bagged and placed in the autoclave to be curried.
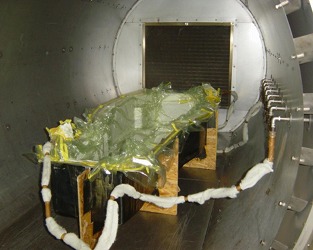
Once this is done, the carbon fibre chassis can be removed from the fibreglass moulds above, and you have your chassis.
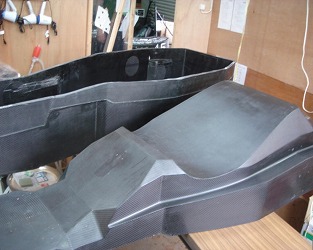
As you can see above, we do our chassis in two pieces (a top and a bottom half:TG03), but some teams do it in a single piece (but its harder and takes much more time:TG04). we just bond the top and bottom halves together to form the chassis.
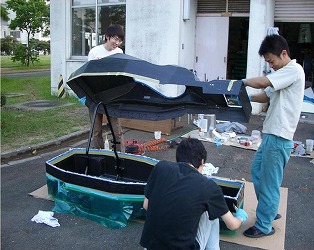
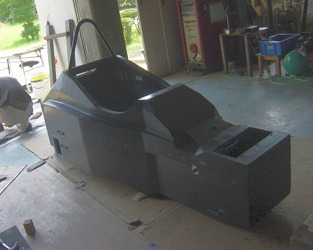
I hope this helps you out anyway……
For analysis, we use a program by the name of ANSYS and MECHNICA(look it up on google). It is quite complex to use, but fine once you have had some experience with it. You can also do all of you other FEA (finite element analysis) testing in this program- we use it for everything.
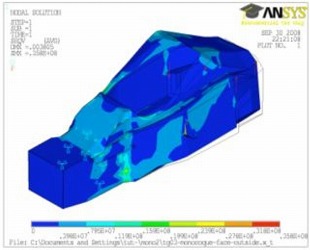
Structural equivalency is a little MORE complex. Basically, everything in the FSAE Rules book which the car must comply with is written for a spaceframe style chassis (like what you are running at the moment). Thus, any rules in which your chassis does not follow from the book, you need to prove that what you have done is just as strong as what is written in the rules book.
Structural Equivalency for a carbon fibre monocoque usually involves setting up a test rig and doing an impact test (say a small portion of the side of the chassis where the drive sits with the roll hoop mounted in). Usually, this is compared to a spaceframe design, and the results need to show that the carbon fibre monocoque can absorb just as much energy (which is pretty easy as it does lots more than the spaceframe). There are also other tests which need to be completed, such as fibre pullout strength- usually a rig is setup to also test these sorts of things.
Anyway, I hope that this information is helpful, and good luck in the future with the carbon fibre monocoque.
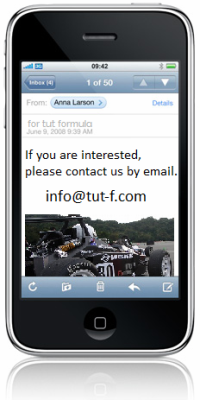
Finally, Here is some additional information which I think you might find useful.
References
1) Braydon, T.H., Darrow, D.C.. 1996, 'A Systems Approach for Improvement of the Manufacturing Process for Composite Honeycomb Sandwich Panels', Proceedings of the 28th International SAMPE Technical Conference, pp 1300-1308.
2) Ji, K.J., Wei, C.Y., Deng, W.H., Zhang, Y.S., Liu, Y.J., Mao, R.Z. and Wang, X., 2002,Evaluation of Glass Fibre/ Epoxy Prepreg Quality During Storage, Polymers and Polymer Composites, vol. 10, no. 8, pp 599-606.
3) Abot J.L., Daniel I.M., 2001, 'Composite Sandwich Beams Under Low-Velocity Impact',American Institute of Aeronautics and Astronautics.
4) Allen, H.G., 1969, 'Analysis and Design of Sandwich Panels', Permagon. Hajime, K., Akira, N., Nobuyuki, O., 2001 'self-adhesive type honeycomb co-cure prepreg'SAMPE Journal, vol. 37, no. 2, pp. 89-92.
5) Thompson, R.W., Matthews, F.L., O'Rourke, B.P., 1995, 'Load Attachment for Honeycomb Panels in Racing Cars', Materials and Design, vol. 16, no. 3, pp. 131-150.
6) Campbell, F.L., Mallow, A.R., Browning, C.E., 1995, ??Porosity in Carbon Fibre?? Composites An Overview of Causes, Journal of Advanced Materials, vol. 26, no. 4, pp. 18-33.
7) Hayes, B. S., Seferis, J. C., Edwards, R. R., 1998, 'Self-adhesive honeycomb prepreg systems for secondary structural applications' Polymer Composites, vol. 19, no. 1, pp 55-64.
8) Burchardt, C., 1998, 'Fatigue of Sandwich Structures with Inserts', Composite Structures, vol.40, no. 3, pp. 201-211.
9) Thomsen, O.T., 1998, 'Sandwich Plates with Through the Thickness and Fully Potted Inserts:Evaluation of Differences in Structural Performance' Composite Structures, vol.42 40, no. 2, pp159-174.
10) Way-Nan Yeh, Ye-Ee Wu, 1991, 'Enhancement of Buckling Characteristics for Sandwich Structure with Fibre Reinforced Composite Skins and Core made of Aluminium Honeycomb and Polyurethane Foam', Theoretical and Applied Fracture Mechanics, Vol15, pp 63-74.
11) Shigley, J.E.& Mitchell, L.D., 'Mechanical Engineering Design', McGraw-Hill, latest metric ed.
12) Society of Automotive Engineers, 2008 Formulae SAE Rules.
13) Thomsen, O.T., Rits, W., 1998, 'Analysis and Design of Sandwich Plates with Inserts - A High-Order Sandwich Plate Theory Approach', Composites Part B, vol. 29, pp795-807.
14) Matweb, [Online], www.matweb.com
15) JIS,[Online]http://www.jisc.go.jp/
By yuya,KUSANO